Used robot cuts costs by half at DFI-Geisler
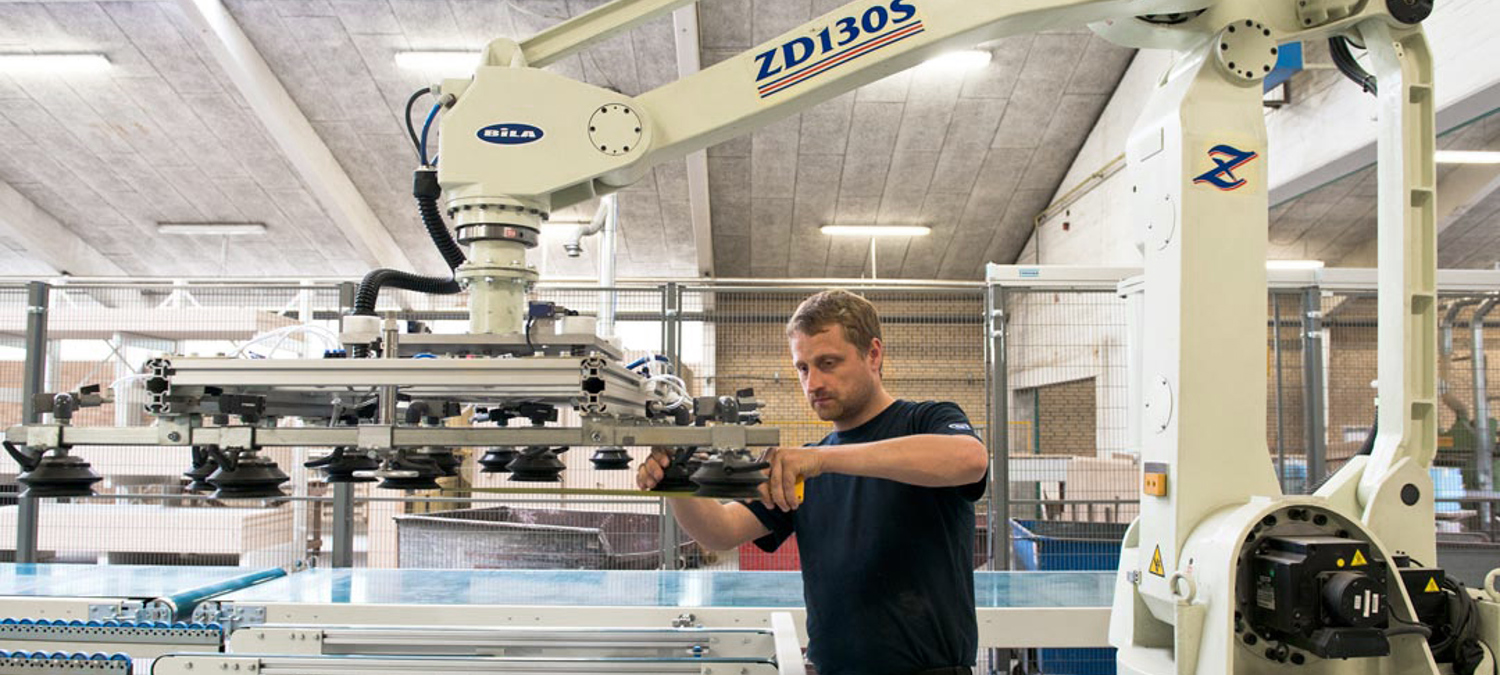
Minimises production time
At DFI-Geisler, the labour requirement has been reduced by a whopping 50%. Today, the entire glue-process is handled by one employee. Associated staff have been involved in the entire automation process, including visits and introduction at the manufacturer.
Increased capacity
Quick ROI in just in 2-3 years
Flexible and reliable solution
Halves production time
Challenge
DFI-Geisler wanted to streamline the process at their glueing system. Two employees were handling the process. One employee manually inserted the heavy tabletops, then another employee manually flipped and pushed them along conveyors.
Solution
Together with BILA Service, DFI-Geisler found a solution to their challenge. The company decided to invest in a renovated robot, which was put into the production chain at the glue system.
Profit
DFI-Geisler has halved the labour requirement with the solution from BILA Service. They have experienced a improvement in production time, while at the same time, they have obtained a future-proof solution that is flexible and has the potential to double capacity.
Investing in flexibility and avoiding bottle necks
BILA Service delivers a renovated robot cell as part of a project for more efficient handling of countertop lamination. DFI-Geisler is one of Europe's leading suppliers of countertops for kitchens, bathrooms, and homes. DFI-Geisler offers countertops in laminate, wood, steel, glass, as well as concrete and has gained a strong position in the European market.
DFI-Geisler faced the production of a laminate countertop series that was labour-intensive and involved many processes. Therefore, they wanted to streamline and rationalise the numerous processes involved in edge bonding countertops with one of the company's edge bonding machines. Previously, two employees handled the bonding process. One employee manually loaded the heavy countertops into the edge bonder, after which another employee manually flipped the countertops using a lifting device and pushed them along connected conveyors.
Renovated robot cooperates with glue system
After DFI-Geisler had discussions with the edge bonder supplier without receiving a potential automation solution, a casual conversation about efficiency possibilities with the supplier and BILA Service turned out to be the solution for the project. The choice fell on an investment in a renovated robot provided by BILA Service, which would collaborate with the edge bonding machine.
"A used robot had the right investment scope for us and was the best solution for the price. BILA Service have delivered a renovated robot that looks and performs like new – and even comes with a warranty,"
Jesper Sørensen, Production Manager
Halves manpower and production time
Today, the labour requirement has been reduced by 50%, with only one employee now able to handle the entire glueing process. Associated employees have been involved in the entire automation process, including visits and introduction at the manufacturer.
"The employees have been very positive about automation. They could see good opportunities, including achieving better ergonomic conditions and no longer needing overtime to keep up with production,"
Kim Østergaard, Workshop Manager
Furthermore, the production time for the countertops in the project has also been nearly halved: "We have experienced a tremendous change, going from a production time of 7 days to now only 4 days. This includes from the start of production until the countertop is ready for shipment. At the same time, we have obtained a reliable solution that is flexible and has the potential to double our capacity," says Jesper Sørensen, Production Manager.
Get 360 degree consultation about your setup, and let us help you elevate your automation aspirations to the next level.
You can contact us at +45 97 71 00 44.
Contact us
We are ready to answer all your
questions and have a non-committal
conversation about the possibilities
with production optimisation in your company.