Robotarm frees up 150 hours in only 4 months
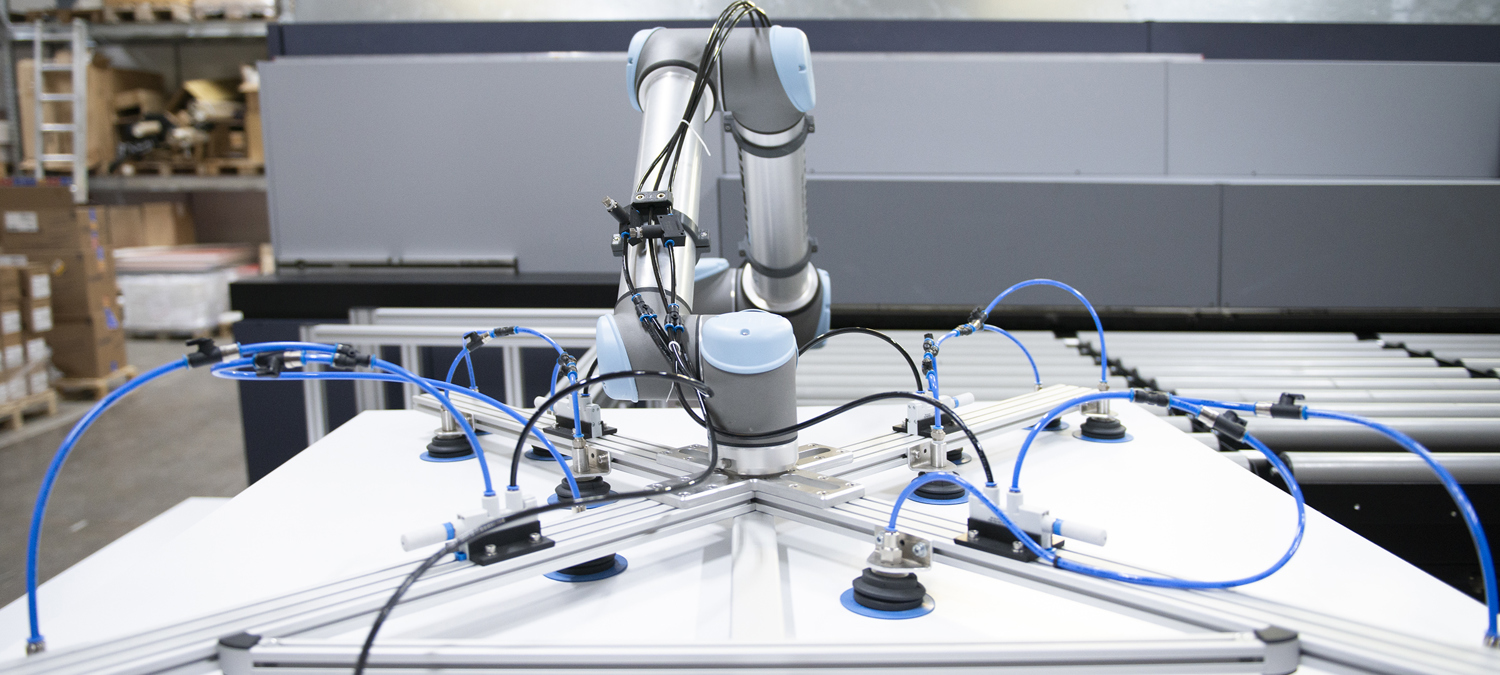
Efficient production
The printing company InPrint A/S has received assistance in their production from a UR10 robotic arm for the past six months. This has resulted in reduced waiting times in production, improved working environment, and released capacity of up to 150 hours over the course of four months.
Freed up 150 hours
Better work environment
Increased competitiveness
Quick installation
Challenge
InPrint A/S experienced significant downtime for their operators when printing large-format designs. The task takes 4 minutes, during which the operator waits for the design to be completed.
Solution
UR10 is the largest robot in the Universal Robots series, boasting a reach of up to 130 cm. With its built-in force mode, the robot arm has the ability to precisely grip plates and move them to the printer.
Profit
The UR robot arm has resulted in reduced waiting time in production, improved working environment, and in just four months, a capacity release of up to 150 hours.
"Streamlined production," "happy employees," "improved physical work environment," and "fantastic investment" are just a few of the expressions Print Production Manager Søren H. Nielsen from InPrint uses to assess the impact of the UR10 robotic arm implemented in the production in October 2016.
"At the beginning, employees were skeptical, thinking, 'What is he doing with this project?' But already after the first week, they could see that this was really good. And now they love it,"
Søren H. Nielsen, Print Production Manager
Too much waiting time
InPrint is a medium-sized printing company with 15 employees, serving as a total provider of printed materials, tackling a wide range of printing tasks. The central Jutland-based print shop often involves many lifts and a lot of waiting time when the machines are printing. However, this collaborative UR10 robotic arm has significantly reduced that since October.
Søren H. Nielsen, responsible for InPrint's large format productions, had been considering for a while where in the production it would make sense to implement a collaborative robot. The answer became apparent:
"In connection with a larger task for a customer, for whom we print large-format designs, it occurred to me that here it would make sense to have a collaborative robot. On such a task, it takes four minutes to print each plate, and in those four minutes, our print operator is just waiting for the machine to say 'beep.' Then he takes out the plate and puts a new one on. And then he waits again. When I walked by him, he mostly just stood there waiting," Søren H. Nielsen explains.
Søren H. Nielsen calculated that the print shop could release two hours daily on such a task by letting a robot take over the manual lifting work of the print operator.
150 hours released in 4 months
In October 2016, he contacted BILA's Area Manager Steen Slabiak Jensen for a quote on the largest robotic arm since the task required a certain reach. The next day, he ordered it, and within three days, the UR10 robotic arm was delivered, allowing Søren H. Nielsen to set up, program, and integrate it with existing hardware himself. He describes the programming and interface as logical and very intuitive.
With a reach of up to 130 cm, UR10 is the largest of the Universal Robots series. It automates processes and manual tasks where precision is crucial. And with the built-in force mode, the robot arm can grip the plates and move them to a unit in the printer so that they are placed precisely.
"We have run 4,500 plates on one machine since December, where the robot handles the plates with an average time of two minutes. This means that since December, we have released a capacity of 150 hours by letting the robot take over. That's equivalent to around 45,000 kroner in released time alone,"
Søren H. Nielsen, Print Production Manager
Improved working environment and increased competitiveness
Employees' skepticism quickly turned to enthusiasm as they witnessed the robotic arm in action. UR10 has not only reduced waiting time but has also streamlined production, resulting in fewer overtime hours, according to Søren H. Nielsen. Overall, the working environment has significantly improved thanks to the robot from Universal Robots: "The working environment has become significantly better. Standing by a machine and just waiting for it to say 'beep' is enough to drive anyone crazy. Now, the person who used to stand by the machine can do something meaningful," says Søren H. Nielsen.
Improved working environment and streamlined production are not the only positive outcomes of the UR10 robot. Søren H. Nielsen also notes that, thanks to the robot's helping hand, the print shop can now take on tasks that were previously impractical – primarily large-scale digital tasks.
"The robot has allowed us to be competitive in tasks that were previously beyond our capacity. Simply because we can now pull a person out and let the robot take over the task,"
Søren H. Nielsen, Print Production Manager
Get 360 degree consultation about your setup, and let us help you elevate your automation aspirations to the next level. You can contact us at +45 9771 0044.
Contact us
We are ready to answer all your
questions and have a non-committal
conversation about the possibilities
with production optimisation in your company.