Eggcelent Factory Performance with Robotic Automation
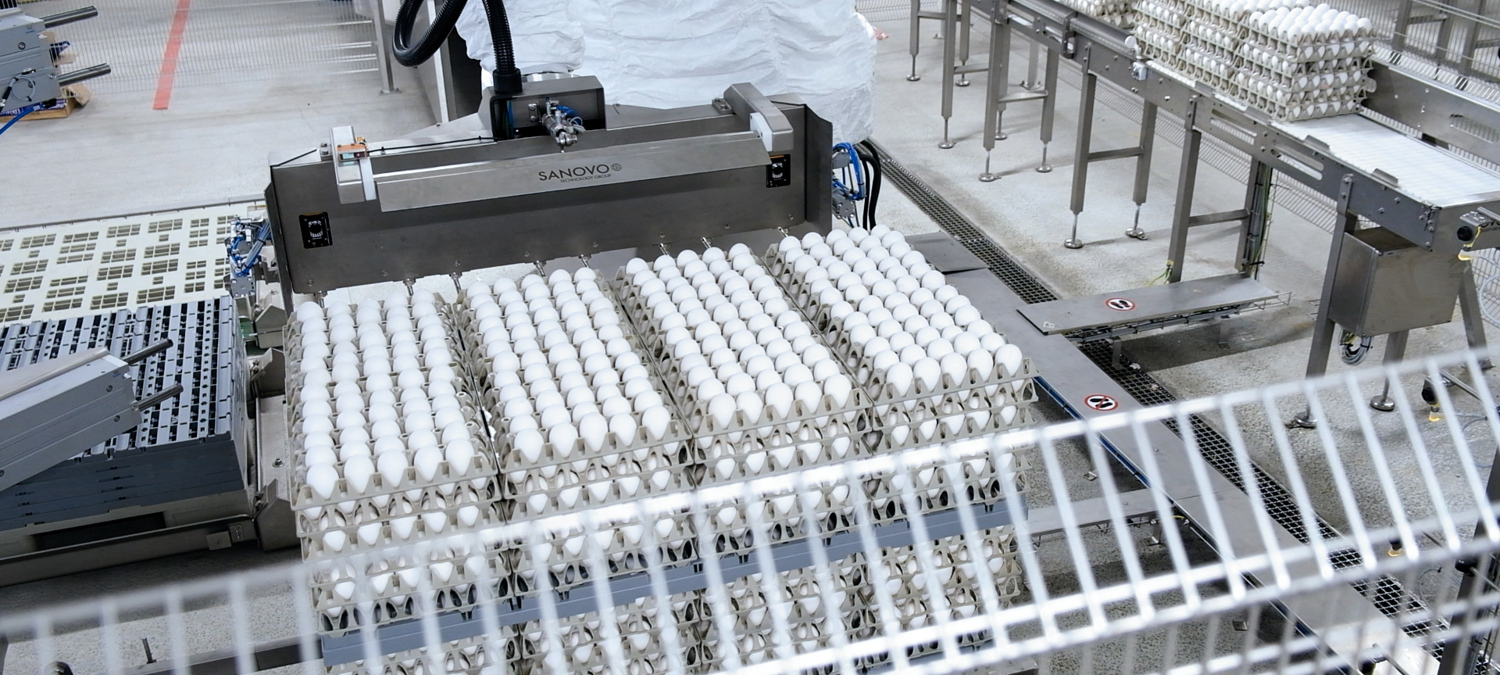
Close cooperation between BILA and Sanovo
SANOVO TECHNOLOGY GROUP is a market leader in the egg processing industry. For more than 60 years, SANOVO TECHNOLOGY GROUP has been a key player in the egg industry and positioned itself as a global supplier of technological solutions across business industries – and Kawasaki Robots have become an important factor in their product portfolio.
Freeing up workers for quality promoting work
Ensuring consistency throughout and higher yield
Increased production capacity
Increased competitiveness
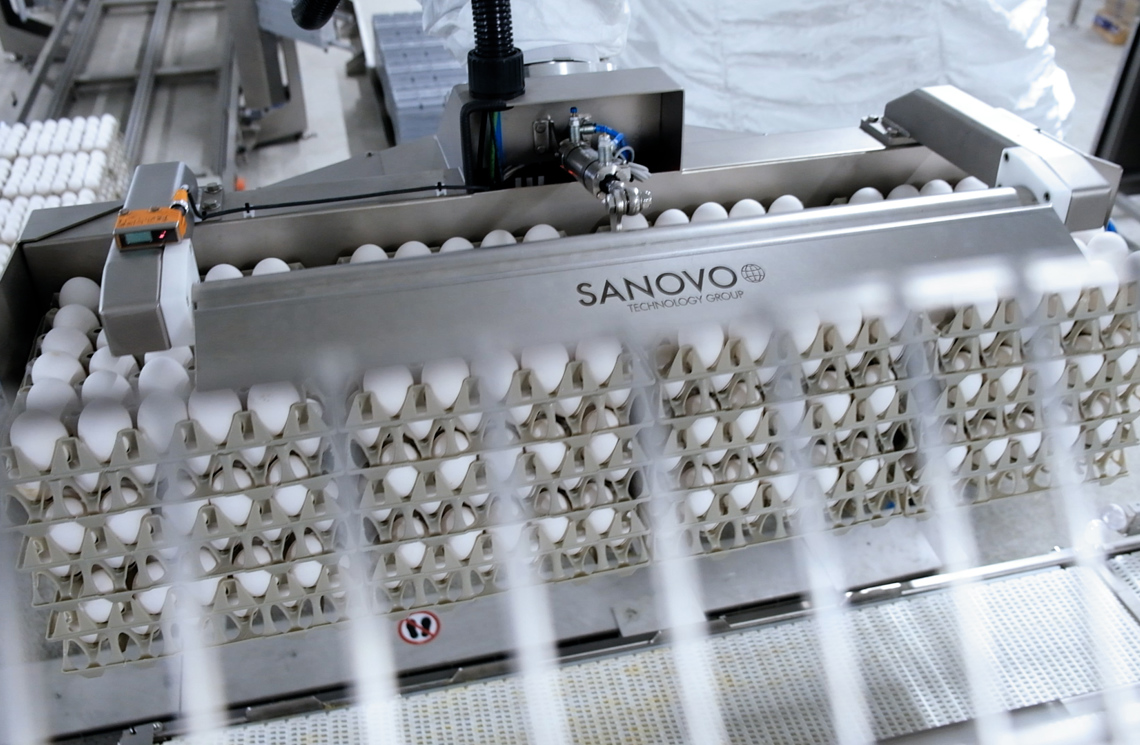
Kawasaki: Eggceptional automation solution
In a modern egg factory, you can almost avoid manual operations by automating the time-consuming elements of the production. Thereby removing the everyday, mundane tasks at factories worldwide, and freeing up workers for quality promoting work.
SANOVO TECHNOLOGY GROUP's robotic automation program offers several efficient and flexible solutions that are a vital part of any modern egg handling and processing factory. However, robotic automation is not only a question of reducing labour. It relates just as much to increasing biosecurity, product quality, and maximising the yield – and at the centre of their robotic automation solutions are robots from Kawasaki.
Equipped with robot arms, SANOVO TECHNOLOGY GROUP's solutions solve everything from palletising and de-palletising to case packing and display loading with high precision and speed. The gripping tool has been developed to be able to support high flexibility in handling different case types and various assignments depending on the need.
“The installation of Kawasaki Robots in our solutions has been an essential factor in increasing production capacity and ensuring competitiveness for our customers,” says Philip Sejling Kogut, Product and Business Manager at SANOVO TECHNOLOGY GROUP.
“The flexibility and efficiency of robotic automation is a vital part of any modern egg handling factory. Automation provides more consistency in the throughput and helps achieve higher yields. Furthermore, it contributes to ensuring high-quality standards in egg production,”
Philip Sejling Kogut, Product and Business Manager
Fleksible robotics for any need
One of the great things about Kawasaki robots is their versatility and flexibility. Kawasaki industrial robots have high-performance technological features, amplified by the power of the controllers and software that can be customised for every industrial automation need.
The high degree of versatility is something SANOVO TECHNOLOGY GROUP benefits greatly from. At the moment, they use four different robots in their solutions depending on the task.
- For case packing in the US, two RS005 robots help pack 30 egg trays into cardboard boxes. The Kawasaki Robots enable the case packing solution to handle up to 160 cases/hour or 57,600 eggs/hour. The RS005 model is one of the smallest R series robots, making it ideal for small-scale material handling applications requiring low payload.
- Case packing is not a one-size-fits-all task. That is why SANOVO TECHNOLOGY GROUP also use the RS007 robot for case packing of packages of different sizes into different types of boxes. The RS007 is easy to adopt for assembly, pick and place, packaging and more. Another great functionality of RS007 is the overdrive functionality meaning the robot can be programmed to move at speeds up the 3x of normal when not carrying a payload. When cycle times are counted in seconds, this is a huge advantage.
- In their de-palletising machines and egg palletising solutions, they use the ZX165 robot. The de-palletising machine gently handles plastic trays of up to 600 cases/hour (216,00 eggs/hour). Known as the workhorses of the Kawasaki Robotics product line, the ZX series is suitable for a variety of applications from assembly to material handling. The ZX series is suitable for harsh environments and can manage a payload of up to 300 kg.
- Designed specifically for palletising, CP300 is ideal for palletising boxes. The case palletising robot can palletise at a speed of 600 cases/hour (216,000 eggs/hour). The CP series feature industry-leading cycle times, a broad motion range, a space and energy-saving controller, and easy-to-use palletising software to program the operation.
Get 360 degree consultation about your setup, and let us help you elevate your automation aspirations to the next level. You can contact us at +45 9771 0044.
Contact us
We are ready to answer all your
questions and have a non-committal
conversation about the possibilities
with production optimisation in your company.