DFI-GEISLER has been Using BILA Service for Maintenance for Over 12 Years
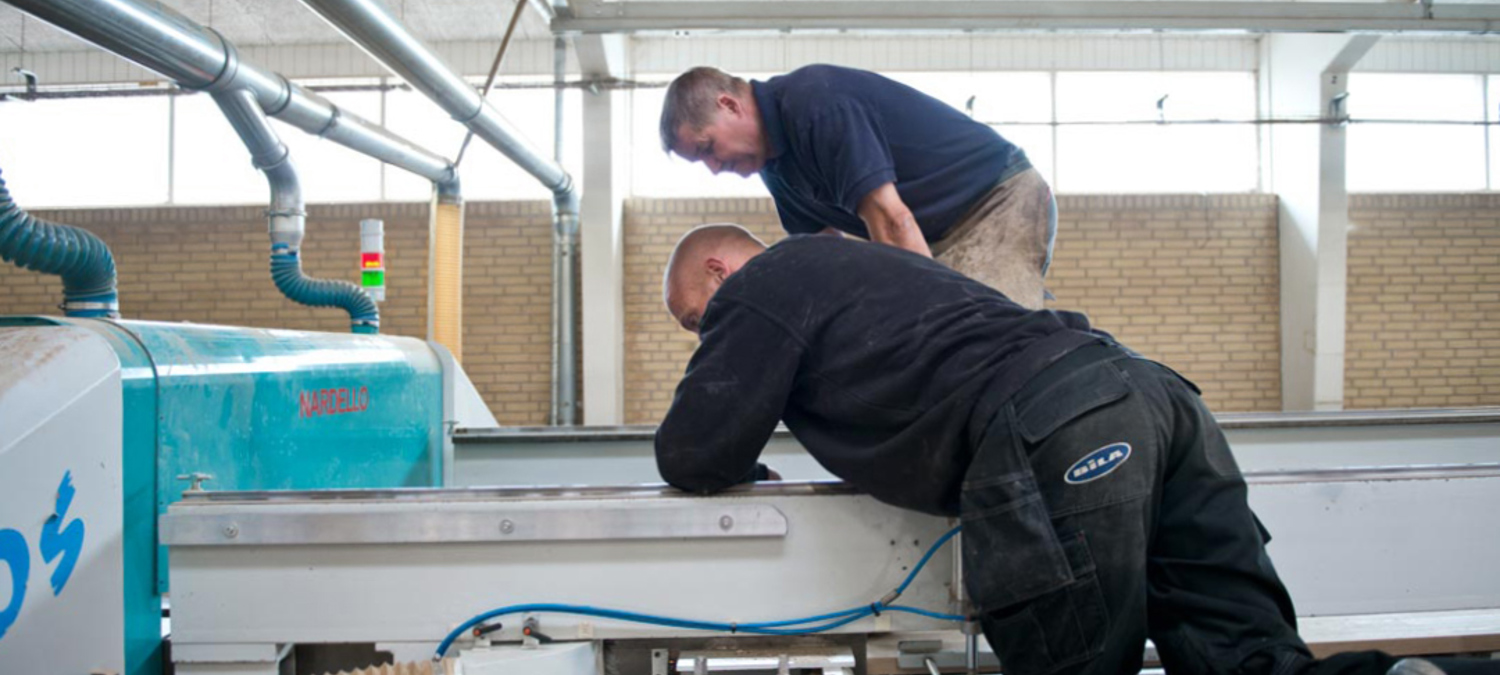
Reliable service for over 12 years
BILA Service keeps DFI-GEISLER operational by leasing skills in a flexible agreement tailored to the customer's daily hourly needs, regardless of the level. DFI-Geisler is one of Europe's leading suppliers of countertops for kitchens, bathrooms, and homes. DFI-Geisler offers countertops in laminate, wood, steel, glass, and concrete, and has gained a strong position in the European market.
Minimal capital tied up in machines and materials
Knowledge and expertise from a large support network
Customised solution based on varying hourly needs
Over 12 years of reliable and economical solution
Challenge
DFI-Geisler sought a durable and reliable solution for maintenance of the company's production. Previously, this task had been entrusted to local craftsmen, but there was also consideration of establishing an in-house maintenance department. However, this would not be particularly cost-effective, as the amount of maintenance needed tends to vary.
Solution
The solution came in the form of a service employee from BILA Service, who takes care of the tasks at DFI-Geisler. The BILA employee is primarily responsible for the tasks at DFI and handles all the necessary maintenance. It is a flexible agreement where DFI-Geisler only pays for the exact number of working hours.
Profit
This solution provides significant economic savings and security compared to having an in-house maintenance department and dealing with fluctuating purchase prices, such as those for steel and iron. Additionally, DFI-Geisler has gained a lot of new knowledge and support. BILA Service is always ready to help, no matter the requirements.
DFI-GEISLER sought an economically sustainable solution
DFI-GEISLER faced a situation over12 years ago where they wanted to find a sustainable solution for the ongoing maintenance of the company. Previously, several local craftsmen took turns handling all ongoing maintenance:
"Economics were crucial, and it is a big advantage for us to have a setup without our own maintenance department. We need a fixed solution that is reliable and cost-effective,"
Jesper Sørensen, Production Manager
Having your own maintenance department involves significant capital tied up in things like machines and spare parts, which may not be guaranteed to be used, Jesper Sørensen elaborates.
Flexibly covers hourly needs
The leasing involves a dedicated employee handling tasks at DFI-Geisler. During the lease, one employee takes primary responsibility for tasks at the customer, gaining significant insight into the customer and contributing the right skills. The employee plans his own day through contact with four supervisors, prioritising tasks based on daily needs.
Jesper Sørensen explains: "If we only have work for 15 hours in a week, BILA covers the rest. If we have work for 50 hours a week, BILA is also responsible for filling in the gaps. It is an incredibly flexible agreement where we only pay for an exact number of hours."
The collaboration evolves continuously
One consequence of the past 12 years of collaboration is that BILA Service's employee has gained significant insight and understanding of DFI-Geisler's business. This has led to the company serving as a consultant, utilised across the organisation. It has resulted in the automation of a gluing process and an investment in three plate inverters, among other things.
On a monthly basis, the customer receives a detailed and clear invoice overview. At the same time, the leasing is evaluated annually, where both parties assess the past year's collaboration and its terms.
"Economically, this solution saves us from uncertainties associated with having a maintenance department and high procurement prices for materials like steel and iron. BILA Service is always ready to help,"
Jesper Sørensen, Production Manager
Get 360 degree consultation about your setup, and let us help you elevate your automation aspirations to the next level.
You can contact us at +45 97 71 00 44.
Contact us
We are ready to answer all your
questions and have a non-committal
conversation about the possibilities
with production optimisation in your company.