Arla Rødkærsbro Automates Mozzarella Production
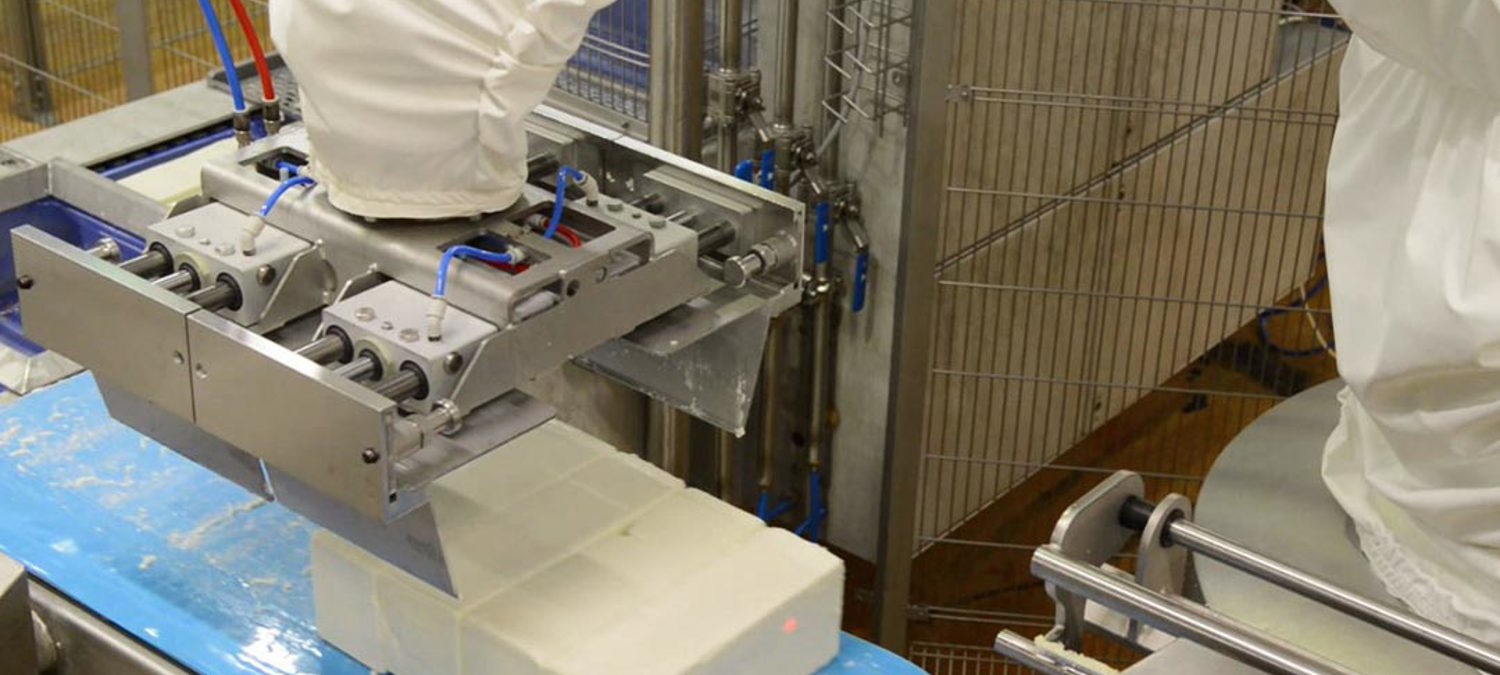
Fully Automated Production
Arla Rødkærsbro is a modern dairy with 250 employees. In Rødkærsbro, Arla has one of Europe's largest mozzarella dairies. A need for greater efficiency arose, and the dairy wanted to streamline their production.
Frees up 3 employees daily
100% customised solution
Fully automated production line
800 blocks per hour
Challenge
The mozzarella dairy wished to further automate its production line. The production line dealt with loading 2.3 kg mozzarella blocks, which involved a highly monotonous and repetitive process. Arla Rødkærsbro aimed to minimise heavy lifting for its employees.
Solution
A new system was installed in the production, along with one featuring a recycled robot. The process involves grouping four mozzarella blocks, after which the first robot picks up the blocks and places them in the thermoformer. Subsequently, the second robot packs the mozzarella blocks into plastic crates, which are then stacked and palletised.
Profit
The solution has fulfilled Arla Rødkærsbro's needs for optimisation by streamlining and automating the production line. This has eliminated the need for heavy and monotonous work, resulting in a reduction in production costs per mozzarella block.
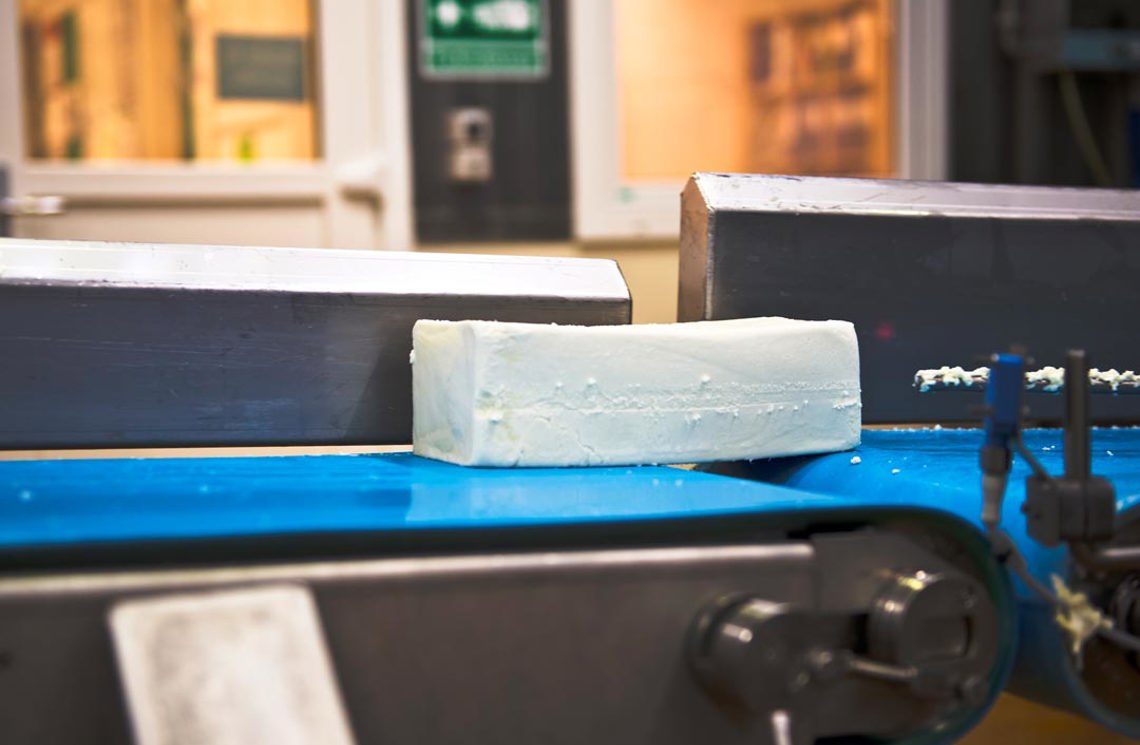
From heavy manual labour to automated and efficient production flow
At the mozzarella dairy in Rødkærsbro, there was a desire to streamline its production line, similar to what had been done on two other lines. Additionally, there was a goal to minimise man-hours, as the manual process involved heavy lifting for the involved employees.
On the production line, the handling of 2.3 kg mozzarella blocks in a thermoformer, followed by manual loading into plastic crates and palletising, constituted a highly monotonous, repetitive task. With these optimisation goals in mind, it became evident to the dairy that automation was a viable solution.
Collaboration has been a key element
”From the start, our dialog has been great, and BILA was consistently testing options, making adjustments, and adapting. The close contact created a sense of security for both parties,”
Bjarke Damsgaard Jørgensen, Production Manager
The solution from BILA comprises the full automation of the mozzarella production line with two robotic systems: a new system and a system featuring a used robot. Approximately 800 mozzarella blocks are packed per hour on the line. Four mozzarella blocks are grouped together, and the first robot subsequently picks them up and places them in the thermoformer. After vacuum packaging in the thermoformer, the mozzarella packages move on, where the next robot packs the mozzarella into plastic crates, which are then stacked and palletised.
Automation frees up 3 employees daily
The investment has met the optimisation goals of the dairy, where the line has been streamlined and fully automated. One person per shift is saved - 3 man-hours per day - from heavy and monotonous work, resulting in a reduction in production costs for each individual mozzarella block.
Arla Rødkærsbro has achieved a well-thought-out solution, tailored 100% to the dairy. The systems have been developed with a focus on design, where the construction of conveyors, hygiene, and cleaning options has been a significant priority. The dairy has been involved from start to finish, requiring that those involved have been in close contact:
”I am very positive about the collaboration with BILA. It has been very beneficial that we have sat physically together. It has been crucial for the result that our collaboration has gone well and smoothly,”
Bjarke Damsgaard Jørgensen, Production Manager
Get 360 degree consultation about your setup, and let us help you elevate your automation aspirations to the next level.
You can contact us at +45 97 71 00 44.
Contact us
We are ready to answer all your
questions and have a non-committal
conversation about the possibilities
with production optimisation in your company.